Show Me Soils specializes in servicing Norweco Singulair alternative wastewater products in the Illinois areas of Shiloh and Belleville. We offer service contracts to you at a reasonable rate; all while keeping accessible, detailed records of your system so you don’t have to. We have two full-time service trucks in the field, staffed by quality technicians who are certified to maintain your wastewater needs.
In the office you will find our knowledgeable staff members ready to answer your call. We pride ourselves in our ability to answer our phones promptly AND by a “real live person!”
You will find two full-time, very knowledgeable staff members in our office ready to answer your telephone call. We pride ourselves on the ability to answer our phones promptly and we guarantee you that “a real live person” will answer the phone!
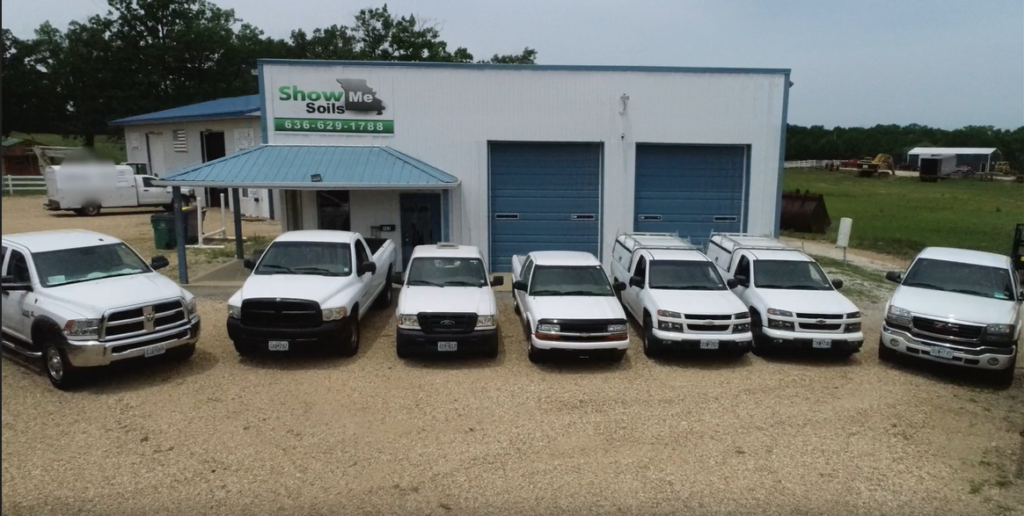
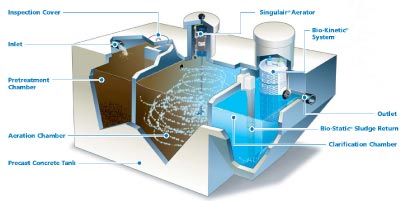
206 Aerator 3 Year Warranty Lifetime Exchange Program
The Singulair system is the state-of-the-art alternative to a troublesome septic tank for domestic waste water treatment. Employing the extended aeration process, the Singulair plant provides flow equalization, pretreatment, aeration, clarification, tertiary filtration and optional chemical addition within a single precast concrete tank. The only mechanical component is the Norweco fractional horsepower aerator, which runs at 1725 RPM and is certified with a 30 minute per hour run time. The patented Bio-Kinetic device is an integral component and assures that all flow through the Singulair system is equalized and completely treated.
Designed for domestic waste water flows ranging from 500 to 1,500 gallons per day, performance of the Singulair system is certified by NSF International and the Canadian Standards Association. Sold only through local, licensed, factory-trained distributors, the Singulair system is backed by Norweco’s three year warranty and lifetime exchange program and insures a safe, sanitary home environment.
Aerator Assembly
The manufacturing and Repair station for our aerators includes all equipment necessary for assembly, testing and quality control. Each aerator is built to precise tolerances and is run through a series of individual tests, evaluating each unit’s performance under actual operating conditions. Safety and quality are emphasized throughout the aerator manufacturing process.
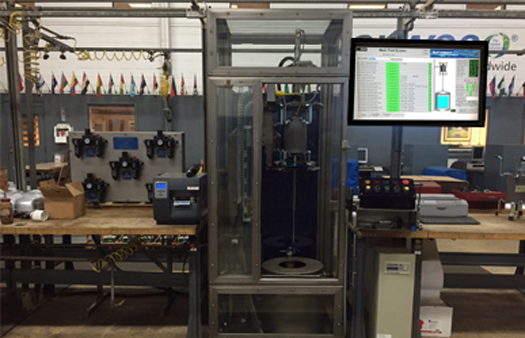
Our Aerator Test Center utilizes the most advanced diagnostic equipment to insure that our stringent quality standards are met. Eliminating human error, it seamlessly performs 40 significant tests in under 1 1/2 minutes. This insures we have accurately measured vibration, motor winding resistance, continuity, voltage, noise level and air delivery.
Below is a list of common practices associated with septic system maintenance. Each system will require a specific servicing which will be correctly completed by our top trained staff who are Factory trained service technicians.
- Clean stainless steel aspirator shaft
- Clean aspirator tip
- Clean fresh air vent
- Inspect aeration chamber contents
- Check operation of control center
- Adjust time clock if required
- Remove the Bio-Kinetic Filter system
- Inspect the clarification chamber
- Inspect the outlet coupling
- Clean the Bio-Kinetic Filter
- Inspect the sludge return
- Inspect the outlet coupling
- Add Chlorine Tablets to the tablet feeder
- Inspect vacuum breakers, pumps and alarms (if applicable)
- The technician may perform additional work. Tests performed and the technician’s observation’s of the system are listed. Specific recommendations may be indicated to help insure the efficient operation of your system.
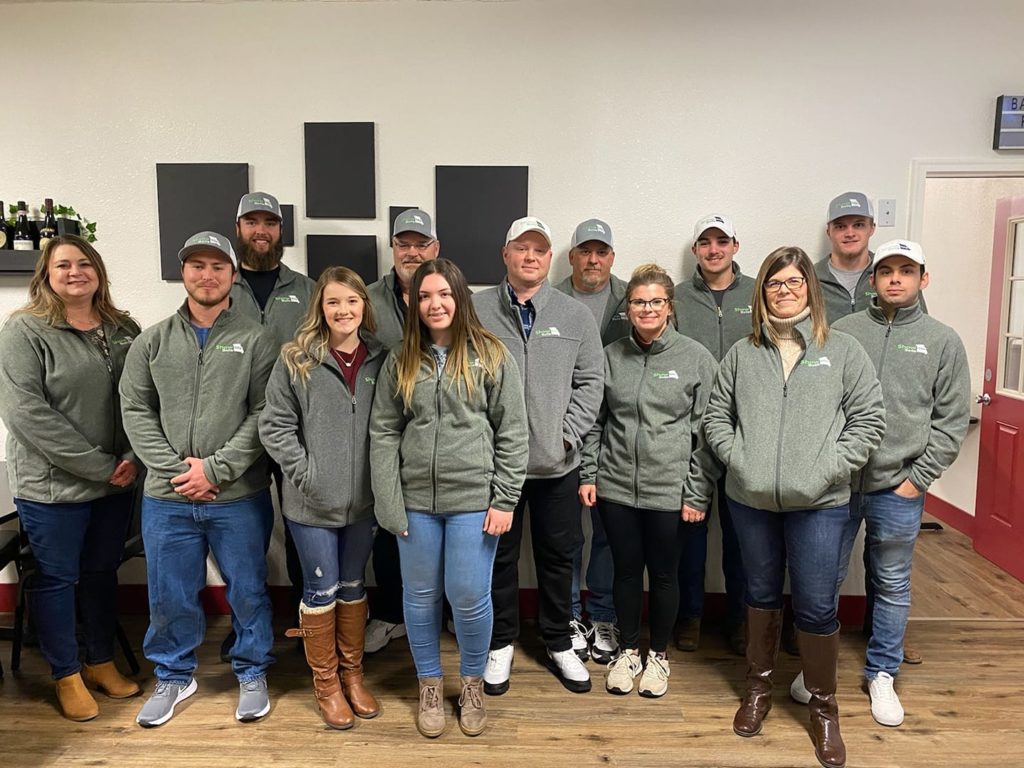